1. Mechanical seal knowledge: working principle of mechanical seal
Mechanical seal is a shaft seal device that relies on one or several pairs of end faces that slide relatively perpendicular to the shaft to maintain fit under the action of fluid pressure and the elastic force (or magnetic force) of the compensation mechanism and are equipped with auxiliary seals to achieve leakage prevention.
2. Selection of commonly used materials for mechanical seals
Purified water; normal temperature; (dynamic) 9CR18, 1CR13 surfacing cobalt chromium tungsten, cast iron; (static) impregnated resin graphite, bronze, phenolic plastic.
River water (containing sediment); normal temperature; (dynamic) tungsten carbide, (static) tungsten carbide
Sea water; normal temperature; (dynamic) tungsten carbide, 1CR13 cladding cobalt chromium tungsten, cast iron; (static) impregnated resin graphite, tungsten carbide, cermet;
Superheated water 100 degrees; (dynamic) tungsten carbide, 1CR13 surfacing cobalt chromium tungsten, cast iron; (static) impregnated resin graphite, tungsten carbide, cermet;
Gasoline, lubricating oil, liquid hydrocarbon; normal temperature; (dynamic) tungsten carbide, 1CR13 surfacing cobalt chromium tungsten, cast iron; (static) impregnated resin or tin-antimony alloy graphite, phenolic plastic.
Gasoline, lubricating oil, liquid hydrocarbon; 100 degrees; (dynamic) tungsten carbide, 1CR13 surfacing cobalt chromium tungsten; (static) impregnated bronze or resin graphite.
Gasoline, lubricating oil, liquid hydrocarbons; containing particles; (dynamic) tungsten carbide; (static) tungsten carbide.
3. Types and uses of sealing materials
The sealing material should meet the requirements of sealing performance. Because the media to be sealed are different and the working conditions of the equipment are different, sealing materials are required to have different adaptability. The requirements for sealing materials are generally:
1) The material has good density and is not easy to leak media;
2) Have appropriate mechanical strength and hardness;
3) Good compressibility and resilience, small permanent deformation;
4) Does not soften or decompose at high temperatures, does not harden or crack at low temperatures;
5) It has good corrosion resistance and can work for a long time in acid, alkali, oil and other media. Its volume and hardness change are small, and it does not adhere to the metal surface;
6) Small friction coefficient and good wear resistance;
7) It has the flexibility to combine with the sealing surface;
8) Good aging resistance and durability;
9) It is convenient to process and manufacture, cheap and easy to obtain materials.
Rubber is the most commonly used sealing material. In addition to rubber, other suitable sealing materials include graphite, polytetrafluoroethylene and various sealants.
4. Technical essentials for installation and use of mechanical seals
1). The radial runout of the equipment rotating shaft should be ≤0.04 mm, and the axial movement should not be greater than 0.1 mm;
2) The sealing part of the equipment should be kept clean during installation, the sealing parts should be cleaned, and the sealing end face should be intact to prevent impurities and dust from being brought into the sealing part;
3). It is strictly prohibited to hit or knock during the installation process to avoid friction damage to the mechanical seal and seal failure;
4) During installation, a layer of clean mechanical oil should be applied to the surface in contact with the seal to ensure smooth installation;
5) When installing the static ring gland, the tightening screws must be evenly stressed to ensure the perpendicularity between the end face of the static ring and the axis line;
6) After installation, push the moving ring by hand to make the moving ring move flexibly on the shaft and have a certain degree of elasticity;
7) After installation, turn the rotating shaft by hand. The rotating shaft should not feel heavy or heavy;
8) The equipment must be filled with media before operation to prevent dry friction and seal failure;
9) For easily crystallized and granular media, when the medium temperature is >80OC, corresponding flushing, filtering, and cooling measures should be taken. Please refer to the relevant standards of mechanical seals for various auxiliary devices.
10). During installation, a layer of clean mechanical oil should be applied to the surface in contact with the seal. Special attention should be paid to the selection of mechanical oil for different auxiliary seal materials to avoid causing the O-ring to expand due to oil intrusion or accelerate aging, causing premature sealing. Invalid.
5. What are the three sealing points of a mechanical shaft seal, and the sealing principles of these three sealing points
The seal between the moving ring and the static ring relies on the elastic element (spring, bellows, etc.) and the sealing liquid pressure to generate an appropriate pressing force (ratio) on the contact surface (end face) of the relatively moving moving ring and the static ring. Pressure) makes the two smooth and straight end faces closely fit; a very thin liquid film is maintained between the end faces to achieve a sealing effect. This film has liquid dynamic pressure and static pressure, which plays the role of balancing pressure and lubricating the end face. The reason why both end faces must be highly smooth and straight is to create a perfect fit for the end faces and to equalize the specific pressure. This is a relative rotation seal.
6. Mechanical seal knowledge and types of mechanical seal technology
Currently, various new mechanical seal technologies using new materials and processes are making rapid progress. There are the following new mechanical seal technologies. Sealing surface groove sealing technology In recent years, various flow grooves have been opened on the sealing end face of mechanical seals to produce hydrostatic and dynamic pressure effects, and it is still being updated. Zero leakage sealing technology In the past, it was always believed that contact and non-contact mechanical seals could not achieve zero leakage (or no leakage). Israel uses slotted sealing technology to propose a new concept of zero-leakage non-contact mechanical end face seals, which has been used in lubricating oil pumps in nuclear power plants. Dry running gas sealing technology This type of seal uses slotted sealing technology for gas sealing. The upstream pumping sealing technology uses flow grooves on the sealing surface to pump a small amount of leaking fluid from the downstream back to the upstream. The structural characteristics of the above-mentioned types of seals are: they use shallow grooves, and the film thickness and the depth of the flow groove are both micron-level. They also use lubricating grooves, radial sealing dams and circumferential sealing weirs to form the sealing and load-bearing parts. It can also be said that the grooved seal is a combination of a flat seal and a grooved bearing. Its advantages are small leakage (or even no leakage), large film thickness, elimination of contact friction, and low power consumption and fever. Thermal hydrodynamic sealing technology uses various deep sealing surface flow grooves to cause local thermal deformation to produce a hydrodynamic wedge effect. This kind of seal with hydrodynamic pressure bearing capacity is called a thermohydrodynamic wedge seal.
Bellows sealing technology can be divided into formed metal bellows and welded metal bellows mechanical sealing technology.
Multi-end sealing technology is divided into double sealing, intermediate ring sealing and multi-seal technology. In addition, there are parallel surface sealing technology, monitoring sealing technology, combined sealing technology, etc.
7. Mechanical seal knowledge, mechanical seal flushing scheme and characteristics
The purpose of flushing is to prevent the accumulation of impurities, prevent the formation of air bags, maintain and improve lubrication, etc. When the temperature of the flushing fluid is low, it also has a cooling effect. The main methods of flushing are as follows:
1. Internal flushing
1. Positive scour
(1) Features: The sealed medium of the working host is used to introduce the sealing chamber from the outlet end of the pump through the pipeline.
(2) Application: used for cleaning fluids. P1 is slightly larger than P. When the temperature is high or there are impurities, coolers, filters, etc. can be installed on the pipeline.
2. Backwash
(1) Features: The sealed medium of the working host is introduced into the sealing chamber from the outlet end of the pump, and flows back to the pump inlet through the pipeline after flushing.
(2) Application: used for cleaning fluids, and P enters 3. Full flush
(1) Features: The sealed medium of the working host is used to introduce the sealing chamber from the outlet end of the pump through the pipeline, and then flows back to the pump inlet through the pipeline after flushing.
(2) Application: The cooling effect is better than the first two, used for cleaning fluids, and when P1 is close to P in and P out.
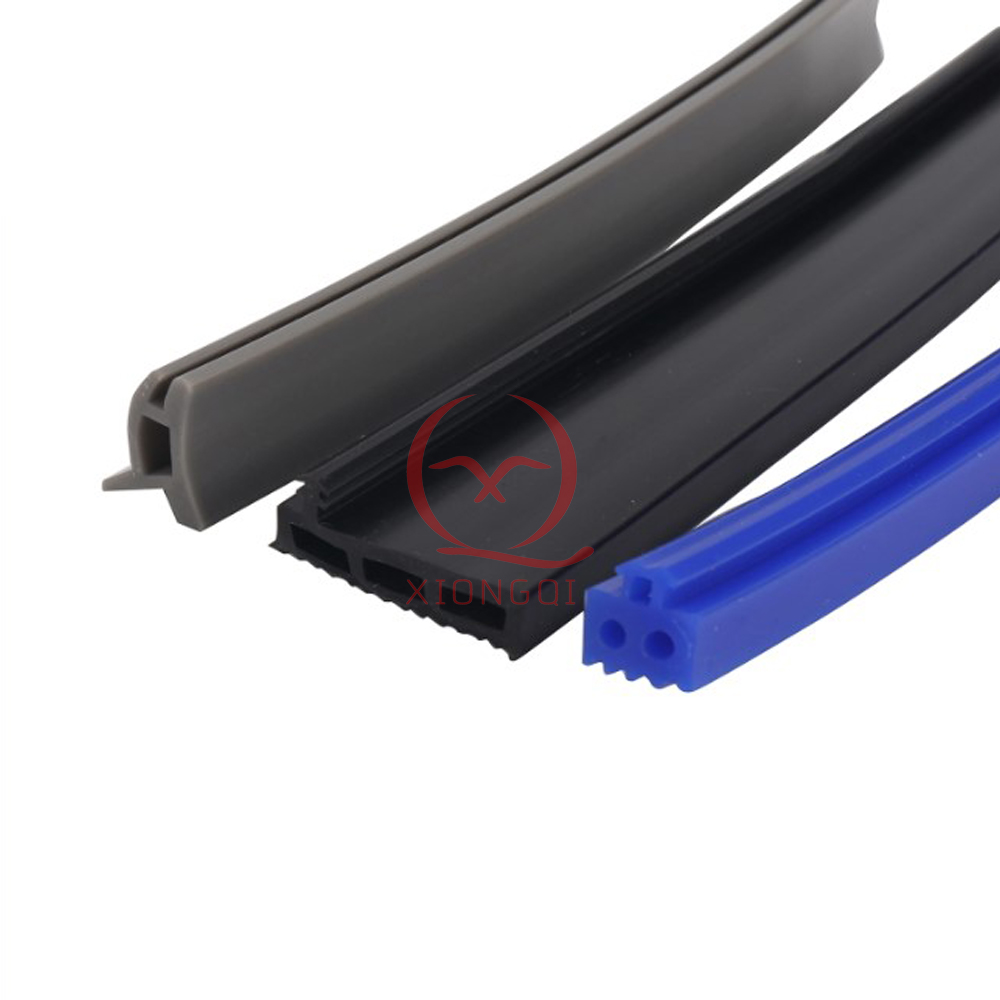
2. External scour
Features: Introduce clean fluid from the external system that is compatible with the sealed medium to the seal cavity for flushing.
Application: The external flushing fluid pressure should be 0.05--0.1MPA greater than the sealed medium. It is suitable for situations where the medium is high temperature or has solid particles. The flow rate of the flushing fluid should ensure that the heat is taken away, and it must also meet the flushing needs without causing erosion of the seals. To this end, the pressure of the seal chamber and the flow rate of flushing need to be controlled. Generally, the flow rate of clean flushing fluid should be less than 5M/S; the slurry liquid containing particles must be less than 3M/S. In order to achieve the above flow rate value, the flushing fluid and the sealing cavity must be The pressure difference should be <0.5MPA, generally 0.05--0.1MPA, and 0.1--0.2MPa for double-end mechanical seals. The orifice position for the flushing liquid to enter and discharge the sealing cavity should be set around the sealing end face and close to the moving ring side. In order to prevent the graphite ring from being eroded or deformed by temperature differences due to uneven cooling, as well as impurity accumulation and coking, etc., Tangential introduction or multi-point flushing can be used. If necessary, the flushing fluid can be hot water or steam.
Post time: Oct-31-2023